A Comprehensive Overview to the Kinds Of Ceramic Covering on the Market
Ceramic layers have emerged as a pivotal solution throughout various sectors due to their special properties and applications. As we explore the unique features and applications of these layers, the effects for performance and longevity end up being increasingly noticeable, increasing questions regarding which kind might finest suit your requirements.
Comprehending Ceramic Coatings
Ceramic layers are innovative safety services that have actually obtained popularity in various sectors, particularly in automotive and aerospace applications. These layers contain a fluid polymer that, when healed, forms a sturdy, hydrophobic layer externally of the substratum. This layer offers improved resistance to ecological pollutants, UV radiation, and chemical exposure, thereby prolonging the life and aesthetic allure of the underlying product.
The basic element of ceramic coatings is silica, which contributes to their solidity and longevity. The application procedure usually entails surface prep work, application of the layer, and treating, which can be achieved via warmth or UV light. When cured, ceramic coatings show exceptional bonding homes, allowing them to stick strongly to a selection of surface areas, consisting of metals, plastics, and glass.
In enhancement to their protective attributes, ceramic finishes additionally use ease of upkeep. Their hydrophobic nature minimizes the adherence of dirt and crud, making cleansing easier and less frequent. Generally, the adoption of ceramic finishings represents a substantial development in surface area security modern technology, offering both useful and aesthetic advantages across multiple markets.
Kinds Of Ceramic Coatings
Different kinds of ceramic finishings are available, each created to fulfill specific efficiency needs and applications - Auto Detailing. The most common types consist of:
Silica-based Coatings: These coatings mostly include silicon dioxide and are known for their resilience and chemical resistance. They are extensively utilized in vehicle and commercial applications.
Titanium Dioxide Coatings: Prominent for their photocatalytic properties, titanium dioxide layers are often applied in settings where self-cleaning and antifungal buildings are preferable, such as in structure products and automobile finishes.
Zirconia Coatings: Defined by their high-temperature security and thermal resistance, zirconia finishings are utilized in applications such as turbine engines and high-performance auto elements.
Alumina Coatings: Displaying superb firmness and thermal stability, alumina coatings are regularly made use of in wear-resistant applications, consisting of cutting tools and commercial machinery. - scratch repair sarasota
Hybrid Coatings: Combining the residential or commercial properties of various products, hybrid finishings use improved efficiency qualities, making them ideal for unique and demanding applications.
Each sort of ceramic finish offers distinct objectives, permitting users to pick the most appropriate option based on certain environmental problems and performance requirements.
Advantages of Ceramic Coatings
Ceramic coatings, in particular, offer many benefits that make them progressively preferred amongst producers and customers alike. These finishes are resistant to scrapes, chemicals, and UV rays, ensuring that the underlying surface stays secured over time.
Along with longevity, ceramic coverings offer exceptional hydrophobic homes, enabling simple cleaning and maintenance. This water-repellent nature reduces the adherence of dirt, gunk, and various other impurities, which can lengthen the visual appeal and performance of the surface area. Ceramic layers can dramatically boost thermal resistance, making them suitable for applications that endure high temperatures.

Application Refine
When using ceramic finishings, a precise strategy is vital to achieve ideal results. The application process commonly begins with extensive surface preparation. This entails washing, sanitizing, and polishing the surface to remove all contaminations, including dust, grease, and prior waxes or sealers. A tidy surface makes certain appropriate attachment of the finishing.
When the surface area is prepped, the following step is to apply Click This Link the ceramic finishing. The finishing ought to be used in thin layers, as thicker applications can lead to uneven surfaces.
After application, the layer needs a certain curing time, usually ranging from a couple of hours to a complete day, depending on the product. Complying with these actions faithfully will make best use of the efficiency and longevity of the ceramic finish, giving a durable protective layer for the surface area.
Maintenance and Durability
To guarantee the durability and performance of a ceramic finishing, regular maintenance is crucial. Ceramic coverings, recognized for their durability and protective high qualities, call for specific care routines to maximize their life-span and efficiency. The first step in maintenance includes regular cleaning with my company pH-neutral soap, preventing severe chemicals that can break down the finish. It is recommended to clean the lorry routinely, preferably every two weeks, to stop the buildup of pollutants that can jeopardize the coating's integrity.
Along with normal washing, regular examinations are vital. Seek signs of wear or damages, such as hydrophobic properties reducing or surface area blemishes. If necessary, a light polish might be used to rejuvenate the covering without stripping it away.
Moreover, the application of a booster spray can enhance the finishing's hydrophobic impacts and recover its gloss. This is specifically helpful for layers that have actually been in usage for an extensive duration. Inevitably, by sticking to these maintenance techniques, one can dramatically prolong the life of a ceramic finishing, making sure pop over to this site that it continues to provide optimal security versus environmental aspects and preserve the visual allure of the vehicle.
Final thought
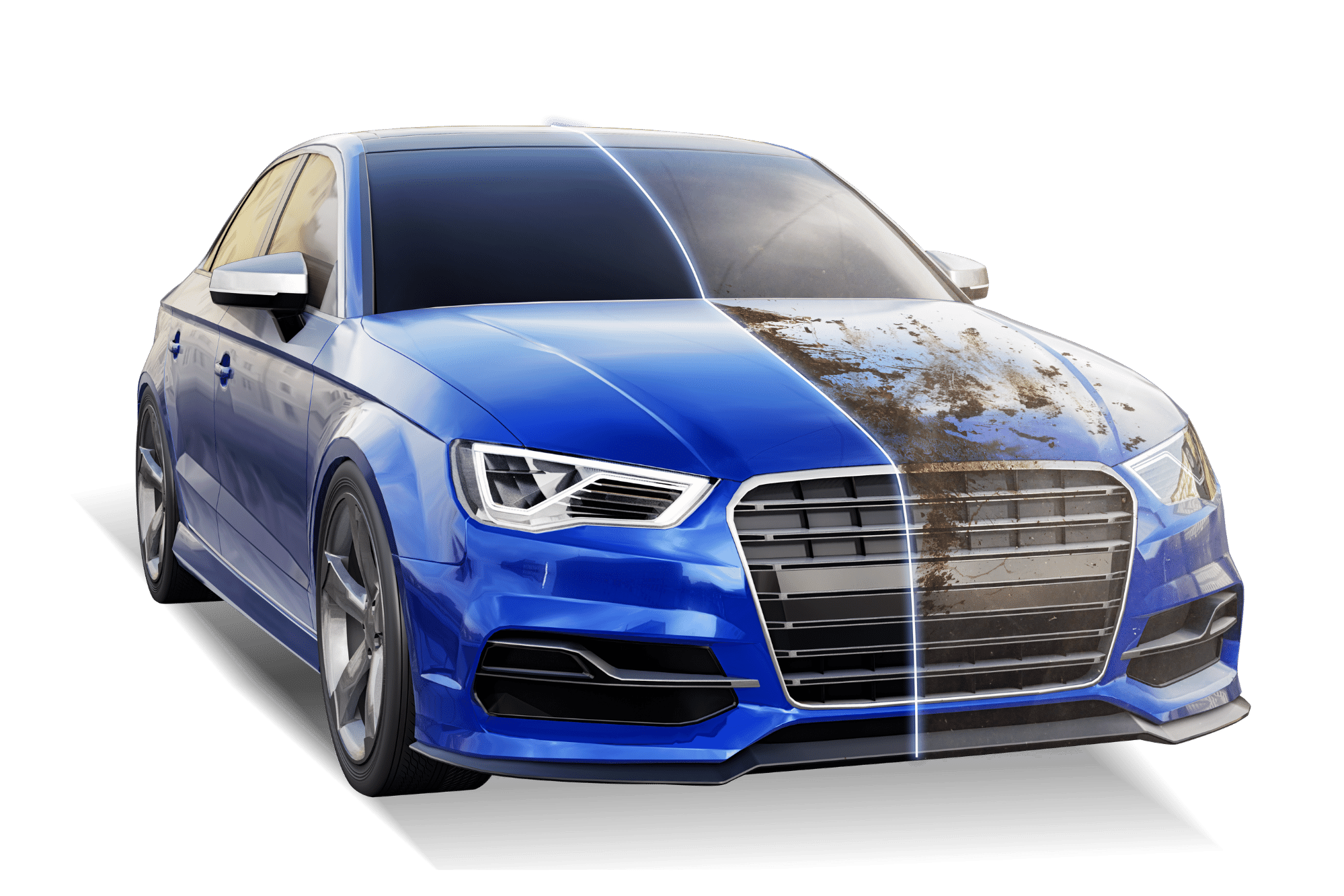